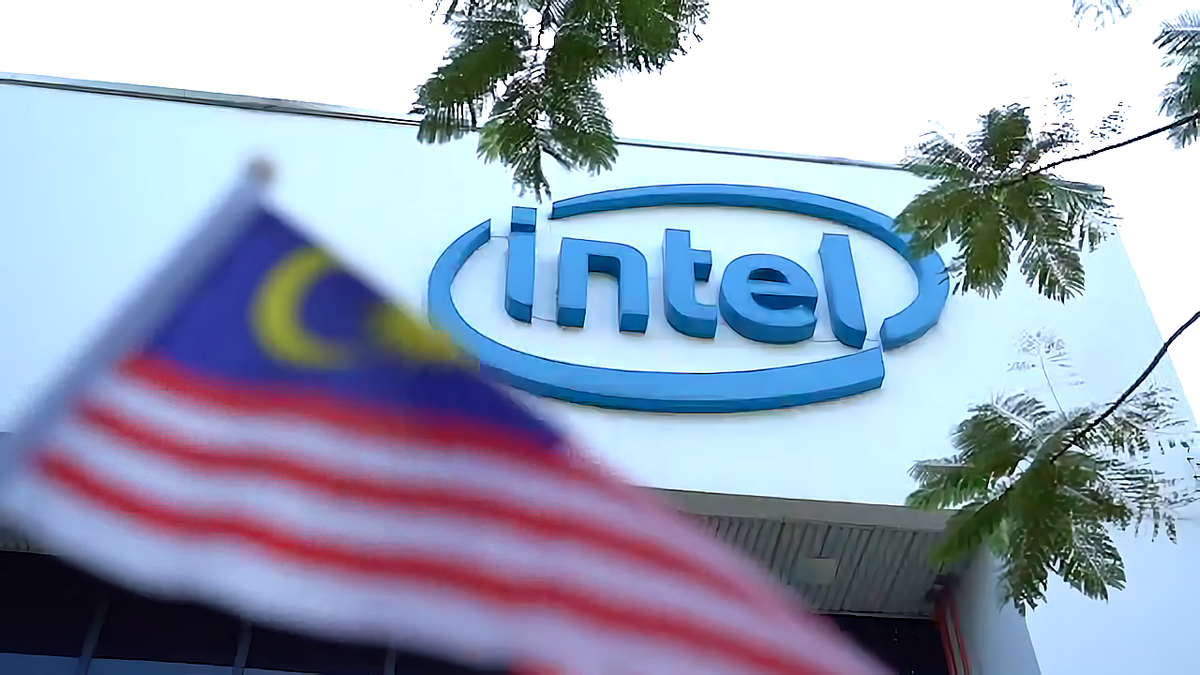
Dans une quinzaine de jours, Intel présentera l'architecture processeur Meteor Lake, garante de l’une des plus importantes évolutions que la firme ait connue sur – au moins – ces dix dernières années. En prélude à cette présentation, nous avons pu visiter l’usine Intel de Penang, en Malaisie.
Première structure installée par Intel hors des États-Unis, le complexe de Penang ne produit pas les fameux wafers à la base des cœurs de nos processeurs. En revanche, en découpant, en testant et en assurant le packaging des puces Intel, l’usine s’inscrit au moins autant dans la révolution Meteor Lake que les manufactures de wafers.
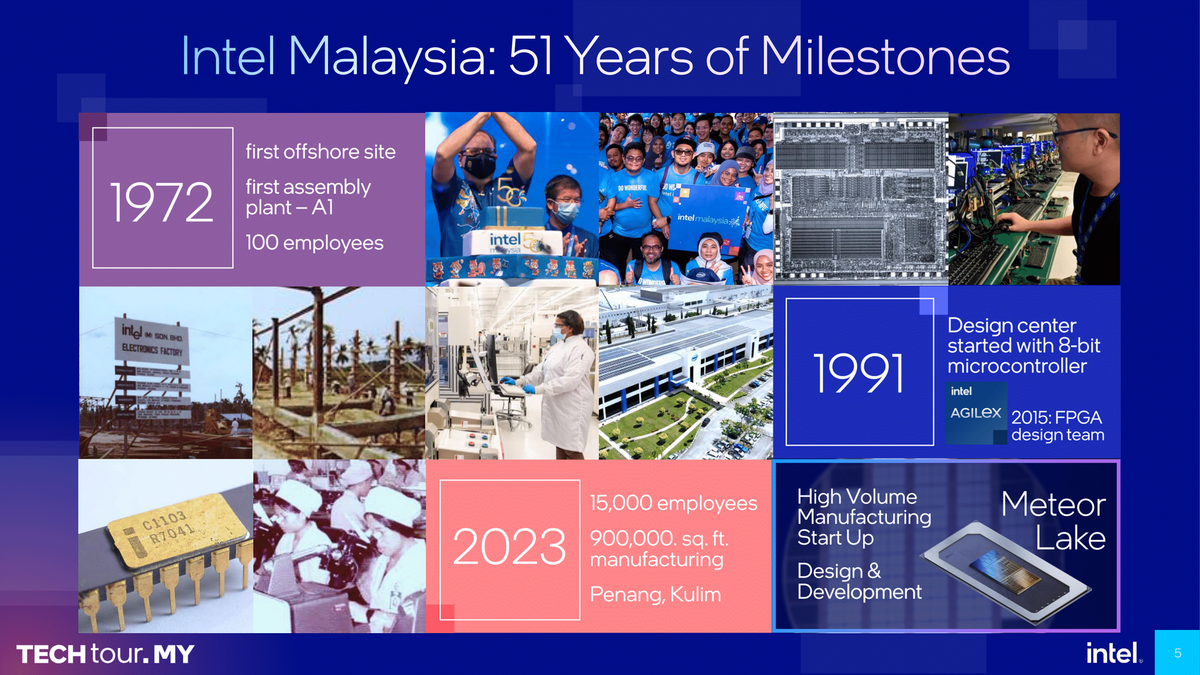
51 ans de présence en Malaisie… mais une implantation mondiale © Intel
Selamat Datang* ! (*bienvenue)
La visite d’installations comme celles de Penang ne se fait pas sur un coup de tête. Ne nous voilons pas la face, il s’agit d’un élément de communication pour Intel qui, après des années d’évolutions pour le moins mineures, semble enfin de retour sur le chemin de l’innovation. La génération Meteor Lake n’est d’ailleurs qu’un élément dans cette stratégie qui vise à redonner à Intel des moyens de production à la pointe et à pleinement prendre en compte de nouvelles techniques de fabrication.
S’il fait partie des plus grands et des plus modernes, le campus de Penang n’est que l’un des dix sites de production estampillés Intel à travers le monde. Par rapport aux établissements irlandais ou israélien, Penang a toutefois la particularité d’être le premier établi hors des États-Unis, preuve du volontarisme d’une région du monde que rien ne prédestinait à la fabrication de puces électroniques parmi les plus avancées, technologiquement parlant.
Une histoire qui ne démarrait pourtant pas sous les meilleurs auspices © Intel
En 1972, lorsqu’Intel décide de s’implanter à Penang, elle fait partie de quelques rares entreprises américaines – parmi lesquelles AMD, les chats ne font pas des chiens – à se laisser convaincre par le gouvernement malais. L’île de Penang n’est alors qu’une zone vaguement utilisée pour l’agriculture et en l’espace de quelques mois, elle devient un centre de production pour puces 8008 – successeur du premier processeur, le 4004 – bien que les techniques de production soient alors nettement moins exigeantes qu’aujourd’hui.
À l’origine, il n’y avait qu’une centaine d’employés sur le site. Aujourd’hui, il s’agit de faire travailler plus de 15 000 personnes réparties entre Penang et Kulim pour un site de plus de 83 000 mètres carrés. Seize bâtiments sont opérationnels et plusieurs extensions sont en construction. Si nous avons eu le privilège de visiter quatre d’entre eux… nous ne pouvions pas prendre de photos, sécurité oblige : les clichés sont donc fournis par Intel.
En cinquante ans, l'évolution du complexe de Penang est impressionnante © Intel
Tri et préparation des cœurs à Kulim (KMDSDP)
Le site de Penang est en réalité partagé en deux. Penang à proprement parler, une île, et une partie sur le continent, à Kulim. Notre visite des installations s’est déroulée dans un ordre inversement chronologique du traitement des puces. Dans ce dossier, nous traiterons les choses en suivant le parcours d’un « processeur », ou plutôt de ses éléments constitutifs depuis leur arrivée en Malaisie jusqu’à leur préparation finale et leur départ.
À Kulim, de l’autre côté du pont de Penang, se déroule la première étape du long parcours des puces Intel. Produits en Irlande ou en Israël par exemple, les wafers sont reçus à Kulim, où ils sont d’abord inspectés. Clean rooms oblige, tous les journalistes ont été contraints de revêtir des combinaisons (les « bunny suits »), mais c’est la lumière ambiante (ambrée) qui surprend le plus : il s’agit de conserver le « collant » des feuilles de mylar sur lesquelles sont disposés les wafers pour être manipulés.
Nous avons l'air malins avec nos bunny suits, mais c'est une précaution indispensable © Intel
Ce que nos hôtes d’Intel baptisent la singulation. Il s’agit dans un premier temps de « tracer » au laser la distinction entre chacun des cœurs. Dans un second temps, via une machine complètement fermée – dommage – les cœurs sont découpés. Des lames à pointe en diamant sont utilisées pour une précision diabolique : les cœurs sont découpés, mais pas la feuille de mylar sur laquelle ils sont encore tous posés. De plus, la galette de wafer est ici immergée afin que les débris soient retirés sans délai et que la température reste basse.
Ainsi découpés, les cœurs de nos futurs processeurs sont acheminés par un système de robots vers la machine de test et de tri à proprement parler. La salle n’a plus ici besoin de cette lumière ambrée, mais les rangées d’unités SDX – des monstres de plus de 500 kg chacune – restent impressionnantes. Chaque SDX comprend une vingtaine d’unités de test et les cœurs sont envoyés individuellement dans de petites unités de plastique.
Préparation des galettes et découpage ultra précis des cœurs © Intel
L’objectif de ces machines conçues en interne chez Intel est de déterminer si pour une série de cœurs prévus, par exemple, pour des Core i9-13900, il s’agira de fournir des 13900, des 13900K ou des 13900KS. Bien sûr, la répartition se fait en fonction de ce que le cœur est capable d’atteindre et d’endurer comme fréquence de fonctionnement par exemple. Remarquez, nos hôtes n’ont pas été très bavards quant au processus exact de tri des cœurs.
De manière plus anecdotique, mais frappante pour le visiteur un peu candide que nous sommes : ces énormes machines SDX se déplacent à la main ! En réalité, elles sont placées sur une espèce de coussin d’air à quelques millimètres du sol : c’est ce qui permet à seulement deux personnes de les manipuler sans difficulté pour en assurer la maintenance par exemple.
Les SDX servent à vérifier un à un tous les cœurs avant leur assemblage final © Intel
Au sein des SDX, plusieurs milliers de minuscules aiguilles sont utilisées pour en vérifier les circuits et constater leurs performances. Dès lors que le SDX donne son feu vert, les cœurs sont placés les uns à la suite des autres sur un très long rouleau qui sert de conditionnement pour la suite du voyage. Que deviennent les cœurs qui n’ont pas été retenus ? Ils sont envoyés au rebut, mais nous avons eu beau demander, impossible de connaître le taux de déchet qui « doit rester le plus faible possible ».
Assemblage et test à Penang (PGAT)
La première partie de notre visite s’arrête avec ces « rouleaux de cœurs » lesquels sont envoyés à quelques kilomètres, dans l’usine de Penang proprement dite. Là, il s’agit d’aboutir aux processeurs que nous retrouverons ensuite dans le commerce au travers de cette phase baptisée « packaging » sur laquelle Intel met maintenant en œuvre ce qu’elle baptise Foveros 3D, une technologie qui s’affine à chaque nouvelle génération.
Les rouleaux, vidés, et les puces au moment de l'assemblage du substrat © Intel
Les rouleaux reçus, le travail peut reprendre. En premier lieu, il s’agit de détacher les cœurs pour les associer à leur substrat, un PCB de couleur verte. Des milliers de microbilles sont utilisées pour lier le substrat et le cœur du processeur puis une machine chauffe le tout à plus de 300°C pour souder la pièce qui, parallèlement reçoit une fine couche d’époxy afin de supprimer le moindre interstice et pour que l’ensemble reste homogène : c’est la « pâte » jaune que l’on voit sur certaines photos.
Arrivé là, le processeur est pratiquement achevé et l’avant-dernière étape consiste à appliquer le TIM (thermal interface material), une espèce de pâte thermique qui joue aussi le rôle de liant pour l’IHS (integrated heat spread), cette pièce que tant d’overclockers s’empressent de retirer pour obtenir de meilleurs résultats. Le processeur est achevé et ne doit plus passer que les tests de « burn-in » pour vérifier son bon fonctionnement et détecter la moindre anomalie.
La phase de pose du TIM et, à droite, l'avant/pendant/après mise en place de l'IHS © Intel
Cette ultime phase est loin d’être anodine et si elle ne peut être considérée comme une partie de la « fabrication » du processeur, Intel déploie d’importants efforts pour vérifier ses puces. Une étape qui n’est pas non plus anodine dans la mesure où elle est associée au binding ou tri des processeurs. Il avait déjà été question d’un tri des cœurs au moment de leur découpage, il s’agit maintenant de déterminer de quelle référence exacte de processeur il est question en fonction de ses résultats.
De hautes températures et de hautes tensions sont appliquées aux CPU sur des périodes de temps… qu’Intel n’a pas souhaité communiquer. Il s’agit de mettre en valeur d’éventuels défauts afin de catégoriser les puces en Core i3, i5, i7 ou i9 par exemple, en fonction du nombre de cœurs opérationnels. Il est aussi question de séparer les puces destinées à la série F – sans solution graphique intégrée – si c’est la partie GPU qui est défectueuse. Ensuite seulement la dernière étape peut débuter.
Aussi moderne soit-elle, une usine a toujours besoin de la vérification humaine © Intel
Après le burn-in, les processeurs sont envoyés vers la plateforme de vérification des performances ou PPV. Elle doit simuler un usage réel des processeurs avec différents cycles de travail sur différents systèmes d’exploitation. Intel n’a pas souhaité détailler davantage cette phase et n’a pas envoyé de photos de la chose. Rappelons d’ailleurs qu’à toutes les étapes de fabrications et de test, ce sont des outils conçus en interne qui sont utilisés donc sous le sceau du secret… industriel.
Avant de clôturer cette visite et de nous renvoyer dans nos pénates, Intel avait un ultime laboratoire à nous présenter : une espèce de cimetière des processeurs. Là, il s’agissait de rassembler les puces envoyées au rebut afin de déterminer pourquoi elles sont défectueuses. Les problèmes peuvent être repérés à différents niveaux de la fabrication et il est crucial pour Intel de comprendre ce qui est arrivé afin de réduire au maximum les pertes.
À gauche, l'imposante machine de test qui est conçue en interne © Intel
Plusieurs ateliers nous ont été présentés en utilisant ici les ultrasons, là l’infrarouge. Chaque atelier est spécialisé dans une tâche particulière. Une machine exploite un véritable sonar pour analyser en profondeur la structure de la puce défectueuse. Les informations recueillies et analysées font ensuite le chemin inverse : elles sont envoyées aux équipes de conception afin d’être prises en compte pour une prochaine révision ou un prochain processeur.
Vers Meteor Lake et au-delà !
Nous n’avons pu assister à la mise en boîte finale des CPU qui, au sortir de la structure de Penang, sont envoyés aux grands comptes pour être intégrés à des ordinateurs complets ou distribués aux grossistes pour la revente au détail. En branle depuis des mois, la chaîne de production dédiée à Meteor Lake devrait connaître son aboutissement d’ici quelques semaines.
Compte tenu de la culture du secret qui entoure la haute technologie, il était difficile de vous faire ressentir comme nous l’avons vécu cette expérience incroyable de visite d’un site de pointe. Nous remercions Intel de nous avoir ainsi ouvert ses portes et nous espérons que, malgré tout, vous en aurez appris un peu plus sur le processus de fabrication de ce qui sera, peut-être, votre prochaine petite folie.