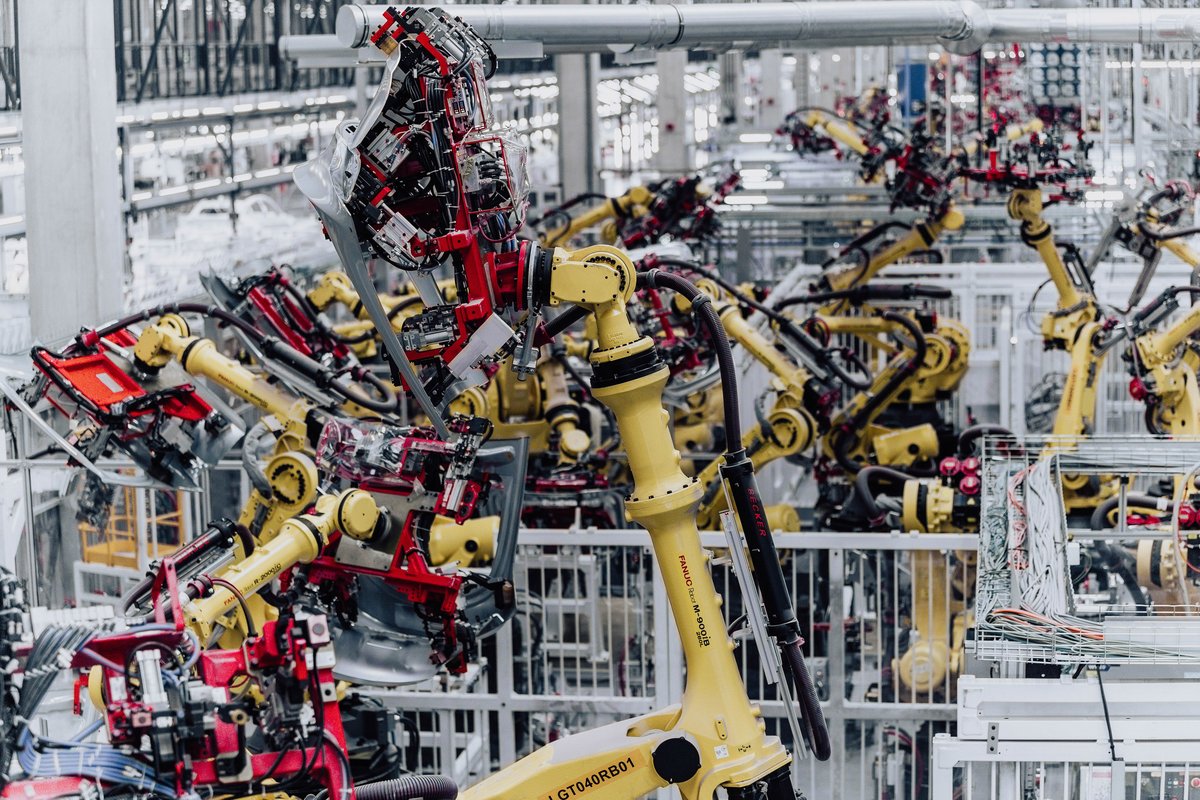
Tesla est sur le point de finaliser un nouveau procédé de moulage sous pression qui pourrait réduire drastiquement ses coûts de production. Si elle y parvient, la firme d’Elon Musk simplifierait la fabrication des véhicules au-delà des capacités du reste de l'industrie automobile.
Au mois de mars, le P.-D.G. de Tesla dévoilait une stratégie de fabrication pour réduire de moitié les coûts de fabrication de ses véhicules électriques. Son nouveau processus est au cœur de ce projet. Il vise à produire la quasi-totalité de la structure sous-châssis complexe d'une voiture en une seule pièce, plutôt qu'en environ 400 pièces distinctes comme c'est le cas avec les véhicules conventionnels. L'impact sur les coûts de production est significatif.
Nouveau procédé de moulage
Le constructeur exploite déjà la technique du « gigacasting » pour la production de son Model Y. Très efficace et rentable, elle implique une utilisation unique de presses massives à très haute pression qui peuvent mouler à la fois les parties avant et arrière du véhicule. Il veut désormais appliquer sa nouvelle méthode à des pièces encore plus grandes, notamment pour la manufacture de sa prochaine voiture électrique à 25 000 dollars, la Model 2.
Reposant sur une combinaison d'impression 3D et de sable industriel, elle modifie le processus de fabrication de moules. Si la création de moules en métal fondu peut coûter des millions pour apporter des modifications simples, expliquant pourquoi la plupart des constructeurs automobiles évitent cette option, Tesla a choisi une nouvelle approche. Avec le sable, l'entreprise construit le moule couche par couche, ce qui le rend plus facile à modifier par la suite.
La firme devrait pouvoir couler un dessous de caisse entier en une seule pièce, au lieu de deux ou plus avec le processus actuel. Elle prévoit de le faire en un seul gigacasting à l'aide d'un nouveau moule qui contient des noyaux de sable solides imprimés en 3D. Après la coulée, le sable est retiré, laissant le même châssis creux sans qu'il soit nécessaire de souder les pièces ensemble.
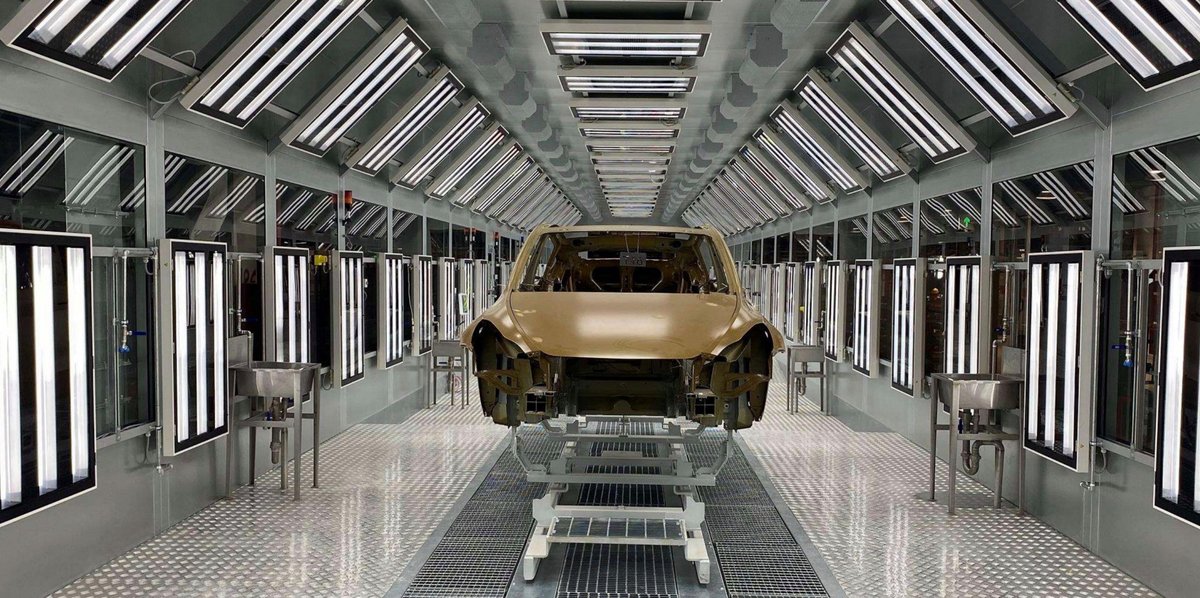
Encore des défis à relever
L'entreprise doit encore relever quelques défis pour pouvoir exploiter son procédé. Elle doit par exemple acquérir des « gigapresses » plus puissantes et de plus grande taille, nécessitant un espace d'installation adéquat. Il s'agit d'immenses machines de moulage sous pression en aluminium fabriquées spécifiquement pour Tesla, à l'origine de la méthode du gigacasting. Elle doit également solutionner le problème de la pression élevée qui peut ne pas convenir à la technique du noyau de sable imprimé en 3D.
Si le constructeur parvient à démocratiser sa méthode dans ses usines, cela lui permettrait de grandement accélérer la production de ses véhicules électriques, et de prendre une grande avance sur le reste de l'industrie. En attendant d'en savoir plus, Tesla a présenté récemment sa nouvelle Model 3.
Source : Reuters